Field Trip! To Fiber First Inc.
I would like to start by thanking Karen at Fibers First Inc. for allowing us to invade her shop and share a better understanding of the process to get commercial roving and yarn from domestic producers. Some of the fibers that we deal with everyday are processed from Fibers First!
Karen greeted us at the door with her big dog Blue happy to invite the Paradise Fibers crew into her mill. The first thing seen upon entering are her two drum carders which take up much of the length of the shop, but we’ll start the tour like she did, at the beginning of the process.
Karen took us to her skirting table. A large slatted table used to shake loose the large debris, second cuts and vegetable matter falling below the table. From there the fleece is pulled as the lower quality fiber is skirted off. This includes parts like the belly and sometimes the neck which are often stained, matted and beyond use. This year Karen is working to teach the local fiber producers community how best to skirt before she starts charging for the extra time it takes to skirt the fleeces. A skirted fleece will last longer without washing, however it is not ideal to leave your fleeces unwashed for long periods of time.
After skirting the fleeces are then sent out to be washed. Karen can’t wash locally due to federal restrictions regarding the waste water which must be evaporated off. Lanolin removed from the fleeces never settles when mixed in the soapy water, so to clean the water it must go through cycles of evaporation.
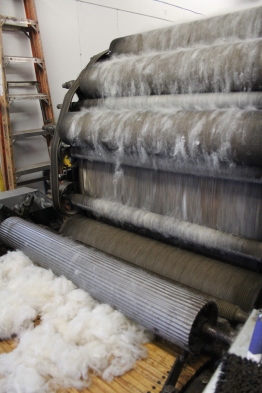
Returned washed fleeces are then sent into the picker. The picker has a protective cover that is so well seated it has a hydraulic lift. The pickers is a 1940’s picker which stretches the fibers without tearing them opening the locks and allowing for smaller vegetable matter to drop out of the wool. The fibers are sprayed with a water oil mixture that cuts static electricity and limits flyways.
The picker shoots the fibers into an enclosed room where now as large clouds of fluff, the wool is collected to be carded.
The machines that take up most of the room in the fiber area are the two congruent turn of the century drum carders the first being a 1919 and the second 1911. The two carders running congruently are half the noise level of the picker taking fluff and turning it into gossamer batts that are slowly pealed of the finest drum on the carder.
The fine batting about a foot wide is then lifted over up and settled into barrels. From here the wool is in an easily spin-able state but for yarn there are quite a few more steps to go.
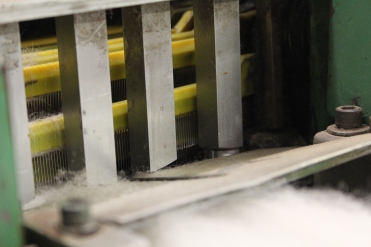
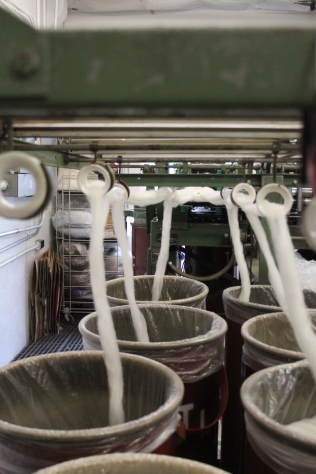
After wool is in long continuous batts it is pulled into a pin drafter. Which uses layers of small delicate combs to pull or draft the fiber into a certain thickness. Sometimes to get the desired thickness the wool is passed multiple times through the pin drafter. It controls thickness as a function of weight over distances.
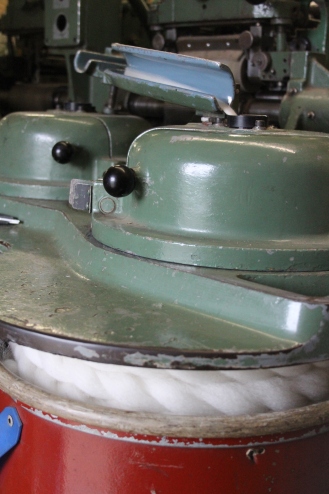
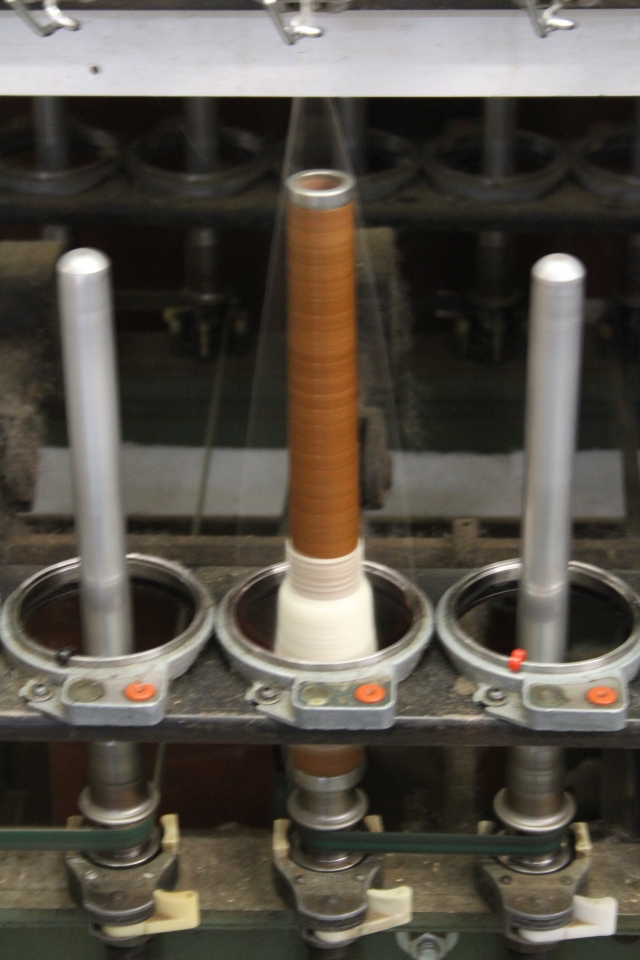
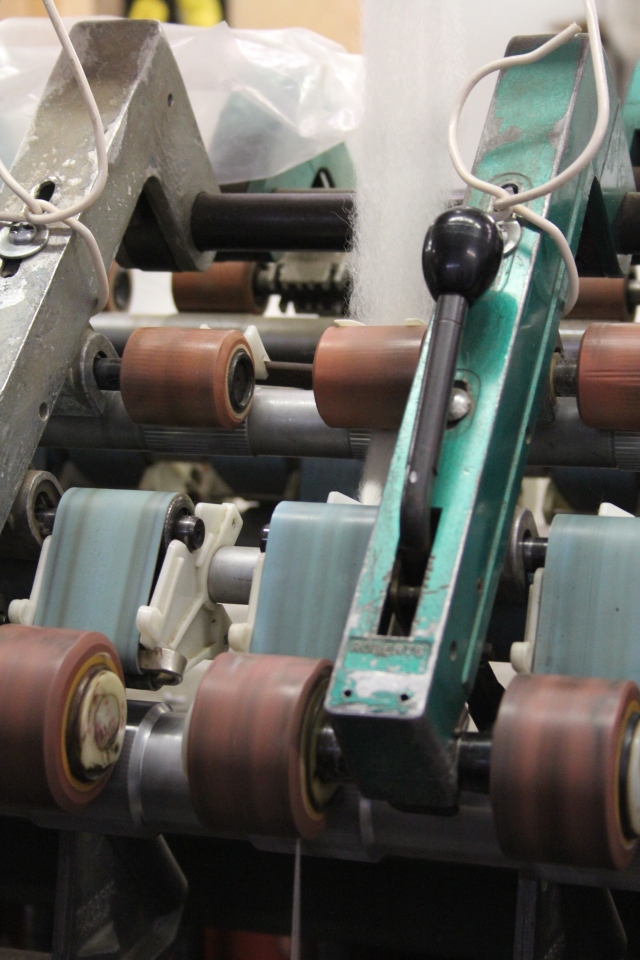
Hand spinners love pin drafted rovings, and here is where most fibers for spinners stop their
processing. However, yarn is the end goal and roving can be spun on her Ring Spinning frame. The Ring Spinning host the spindles below with drafting rollers above. The rollers have independent speeds with the back rollers steadying and feeding the fibers and the front rollers moving faster pulling to thin and align the fibers. The thread guide feeds into the spinning assembly that threads into a D ring called the traveler, which moves around the outer ring giving the machine its name. The thread is then attached to be loaded onto the spindle.
When a few spindles are full they are hung above and then set to ply, the numbers of bobbins going into one strand dictate the ply.
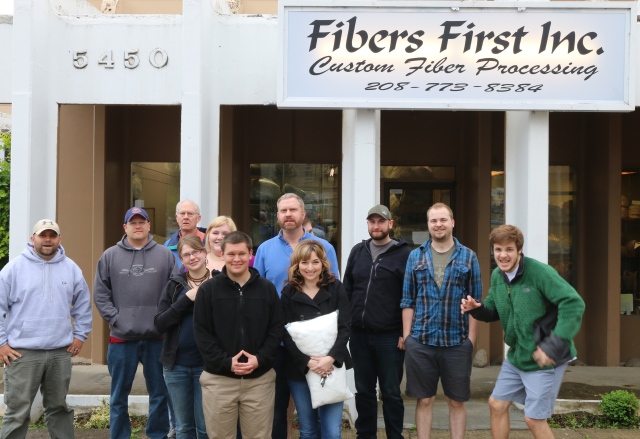
This is wonderful way for the fiber community to connect with individual breeds, fiber characteristics. Single fleeces or flocks can be processed giving clear connections to individual animals. Furthermore fibers can be specialized with blending which can occur at many different stages. From picker, carder, pin drafter and spinning to create unique and diverse fiber combinations. We were watching 80/20 local Alpaca Wool at three different stages.